Rubber components for the energy sector
AVK GUMMI develops, produces and sells rubber components for the energy sector. This includes a wide range of articles – e.g. moulded hoses for contact with gas, oil and bio-based fuel and gaskets for use in battery and fuel cell technologies. Finally, wind and solar energy, including offshore, is part of our area of expertise. With such a wide field of applications, clearly there will be many different requirements concerning function and approvals. As safety is always our number one priority, one common feature is high demands on quality and documentation.
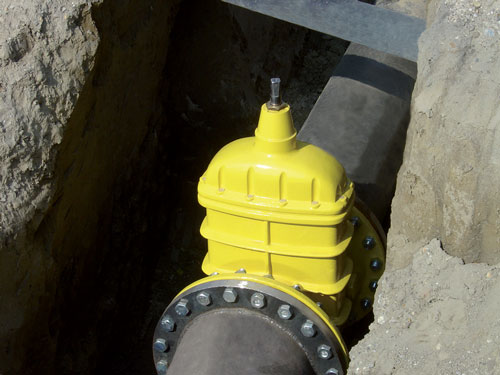
Rubber solutions for natural gas and oil
Rubber that is exposed to natural gas must of course be suited for the purpose. If natural gas can leak through the rubber gasket or be extendedly absorbed by the gasket, the function of the gasket will fail. Such a failure would put the surroundings at risk, and therefore rubber for use in natural gas applications is subject to stringent requirements all over the world. Rubber that is exposed to oil is subject to many similar requirements. However, since we also produce components such as moulded hoses for oil lubrication of chain saws, the equipment manufacturers often have specific approval requirements.
Rubber solutions for fuel
Fuel is not just fuel, and many new types of bio-based fuel have entered into the market during recent years. Fuel must always be handled in a controlled manner irrespective of the climate or other conditions. We develop rubber compounds that comply with the many different requirements, and we are happy to assist you with advice concerning the possibilities and restraints.
Rubber solutions for battery and fuel cell technologies
A battery consists of electrodes and an electrolyte. Depending on the technology, electrodes and electrolytes can pose a challenge in the process of formulating a rubber gasket with the right sealing properties to prevent leakage from the battery. The components can be based on organic solvents or acidic solutions or they can be bound in a more or less fixed structure, which means that the requirements on the rubber compound – not least concerning safety – can differ quite a bit. Furthermore, design and assembly properties may require the combination of rubber with other components, and finally the lifetime of the battery must be satisfactory. All in all, there are many different requirements on the gasket material.
Therefore, the following factors are important:
- The rubber compound must be suitable for the chemistry applied, the operational conditions and the expected lifetime.
- The rubber compound must not release substances that may affect the function of your equipment.
- The rubber compound must have the right approvals, e.g. for contact with natural gas.
- The material properties of the rubber must provide optimal function, such as minimal friction, in order to ensure proper activation of the valve in a gas pipeline. As opposed to liquid mediums that help reduce friction, and with that the closing torque, high friction can be a challenge in gas.
Which type of rubber should you choose?
This depends on the nature of the application. For instance, a shock absorber in a windmill nacelle requires high strength, good cold flexibility, good bonding with metal, etc. Here, an SBR/natural rubber would be a good choice. In contrast, a gasket for contact with biodiesel requires a special rubber, such as NBR or even FKM. Naturally, compliance is an important aspect; in which country will the product be used, and in which markets will you launch the product?
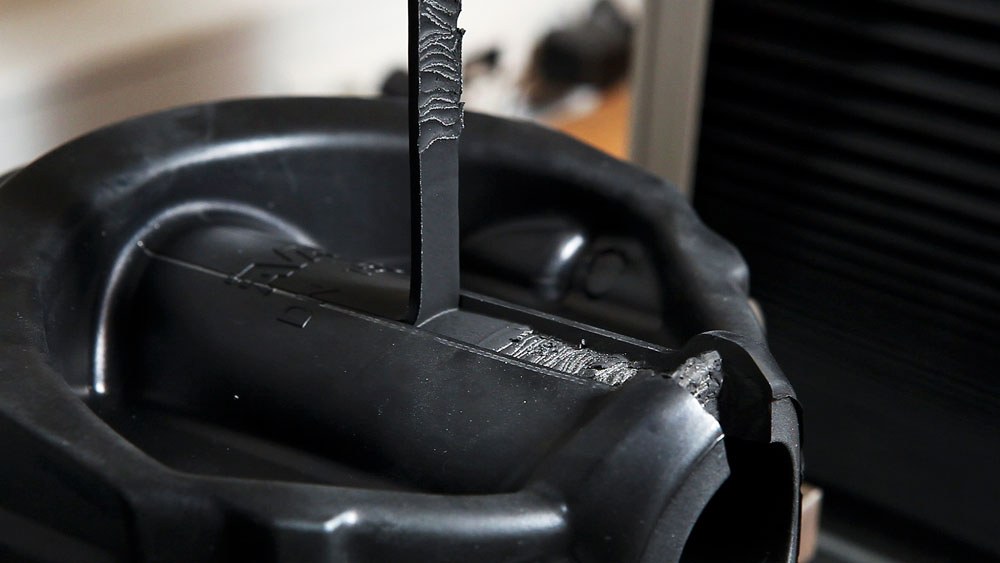
IPR – ownership of your rubber solution
When we develop a new compound, we use this for as many products as possible. However, if we develop a compound for you and this is critical to your business, we can enter into an exclusivity agreement.
The tool that we design for the production of your item is based on your product design and our unique tool design. You will always own IPR of the product design.
Transparency concerning the allocation of IPR is your guarantee that our collaboration will give you a competitive edge and secure your know-how.
The primary types of rubber for the energy sector are, among others:
- NBR for gas, oil, fuel and fuel cells
- HNBR for oil and fuel cells
- FKM for fuel
- EPDM for batteries
- Silicone for high voltage
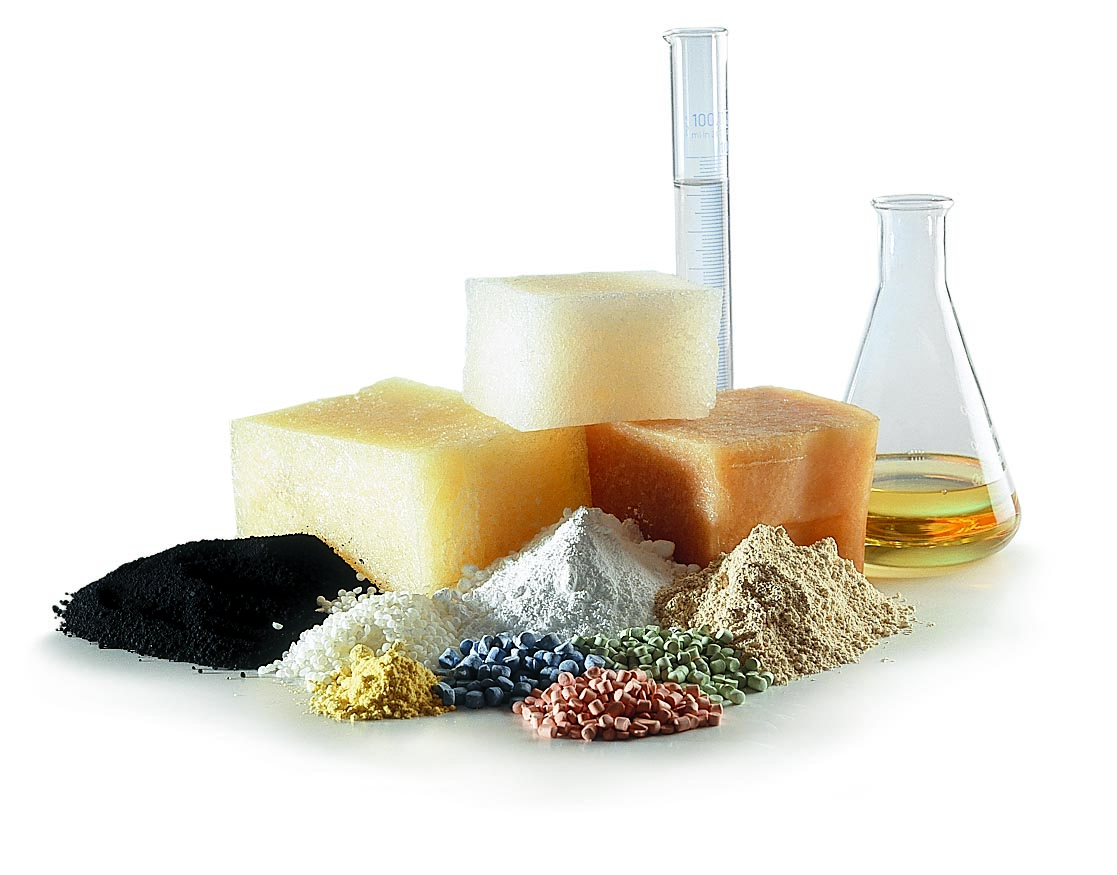
Security of supply through advanced production
When the supply chain is challenged in a global market, you and your customers are highly dependent on your suppliers. Will you receive the products at the right time and price?
AVK GUMMI offers you security of supply in an insecure world.
We consider ourselves particularly strong within the following parts of the supply chain:
- We cooperate with large, well-reputed suppliers. Naturally, price is always an important aspect, but we must never compromise on quality, security of supply or CSR.
- We have one of the world's most advanced, fully automated mixing plants where the raw materials are weighed and dosed with the greatest precision. This enables us to manufacture rubber compounds of a uniquely high quality and uniformity.
- With our complete pilot plant, development, up-scaling and validation processes are carried out in an efficient and safe manner.
- We make sure that we have the right foundation for production, including the right tooling solutions. Furthermore, we always carry out a thorough validation of each manufacturing step before release for production. This is your guarantee that you always get the agreed and expected quality.
Traceability in our production
We have the tools for quickly detecting, correcting and documenting any errors in the unlikely event of an issue with your rubber component.
We collect all relevant process data throughout the entire manufacturing process. The data is stored for 25 years. Together with date marking and material identification on the parts, this forms the backbone of our traceability.
Safety through certifications
Our certifications are your guarantee that we live up to our own high standards. We always focus on safety, quality and the environment, which means that you can fully concentrate on your product without having to spend time on supplier audits. If, however, you should to carry out an audit, you are always welcome!
At AVK GUMMI, we are convinced that focusing on quality, occupational health and the environment pays. Our quality management system is certified in accordance with ISO 9001 and IATF 16949.
In addition, we have an extraordinarily clean and safe production environment certified in accordance with ISO 45001. In 1991, as one of the first rubber manufacturers in the world, we obtained an environmental certification in accordance with ISO 14001.
Read here: Certifications and quality and environmental policies
Consumer safety in a global perspective
If your company operates in multiple markets, you know all about the challenge of complying with the different legal requirements, recommendations and standards – and the burden that comes along with the obligations of documentation.
We send our rubber formulations and test samples to independent, accredited test institutes for testing.
This list shows a selection of the many standards fulfilled by rubber compounds from AVK GUMMI:
- EN 682 GBL
- EN 549
- GB/T 23658
Product development with focus on you and your product
If you are looking for competent advice to improve your product, we are here to assist you. Often we can challenge you with new ideas that you may not have thought of. We are also happy to participate in the development of a new product right from the start – without taking over your design process.
Our focus is to transform your product requirements into concrete development parameters. This may be in the form of mechanical performance criteria, such as damping or documentation of ageing properties, to support your stability data.
With our competent advice as well as our development and production process, you and your product are in safe hands.